How is a bat gate different from other types of cave or mine closures?
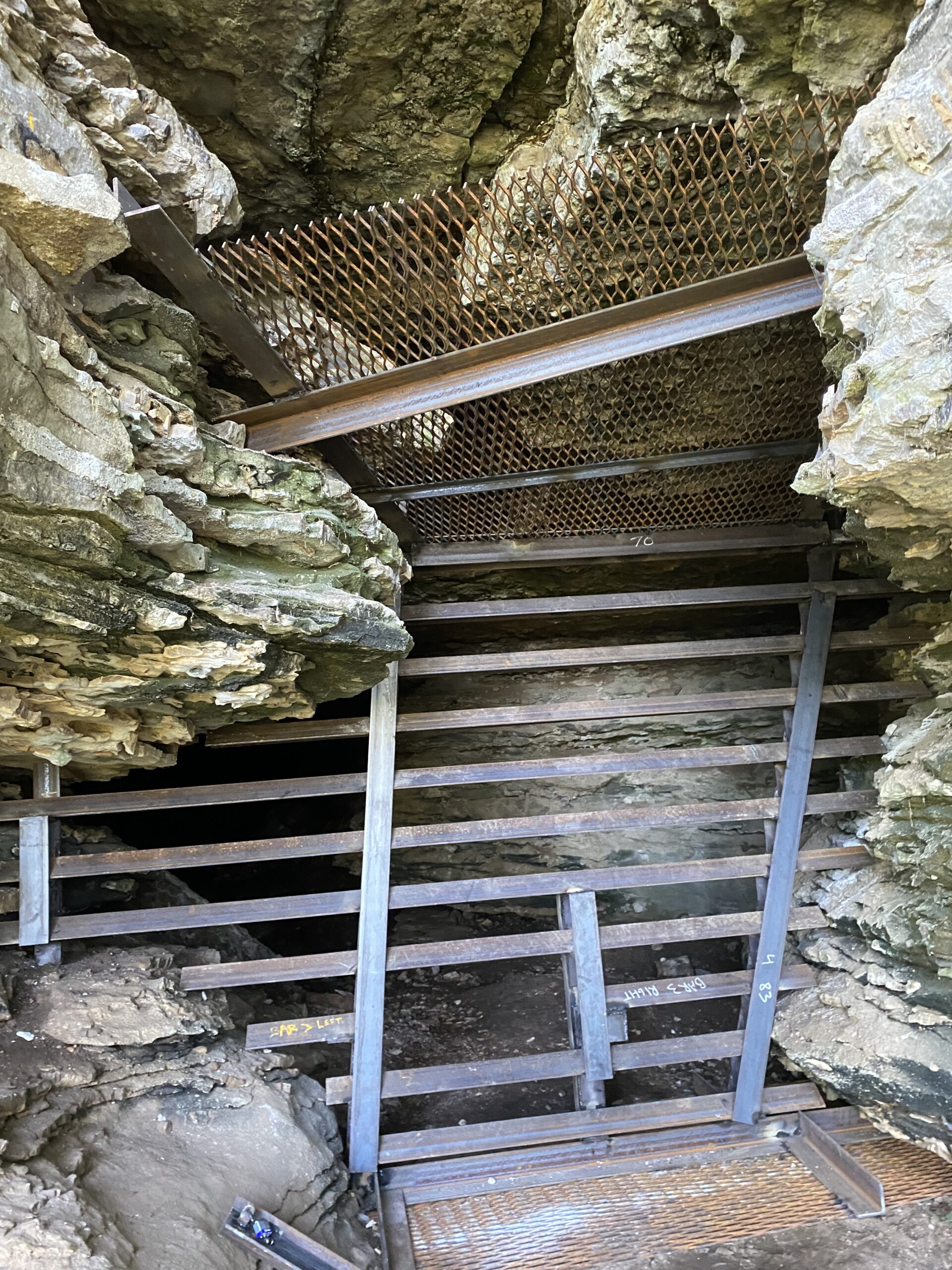
As experts in cave and mine closures, we often receive questions about “cave gates,” “mine gates,” or “bat gates.” These terms can often be used interchangeably, depending on the situation. Our extensive experience in constructing hundreds of gates across the United States has shown that a well-designed and secure gate is crucial for protecting cave and mine resources, including endangered bat species.
Years of research by organizations such as the American Cave Conservation Association, Bat Conservation International, and the US Fish and Wildlife Service have helped to establish an industry standard for bat gates. This standard design, along with accepted variations, is widely recognized and utilized by federal agencies, NGOs, and state wildlife agencies. Our designs use best management practices for bat and mine closures, and we stay up to date with the latest advances in techniques and designs to ensure the highest level of ecological transparency and resource protection.
Why Gate?
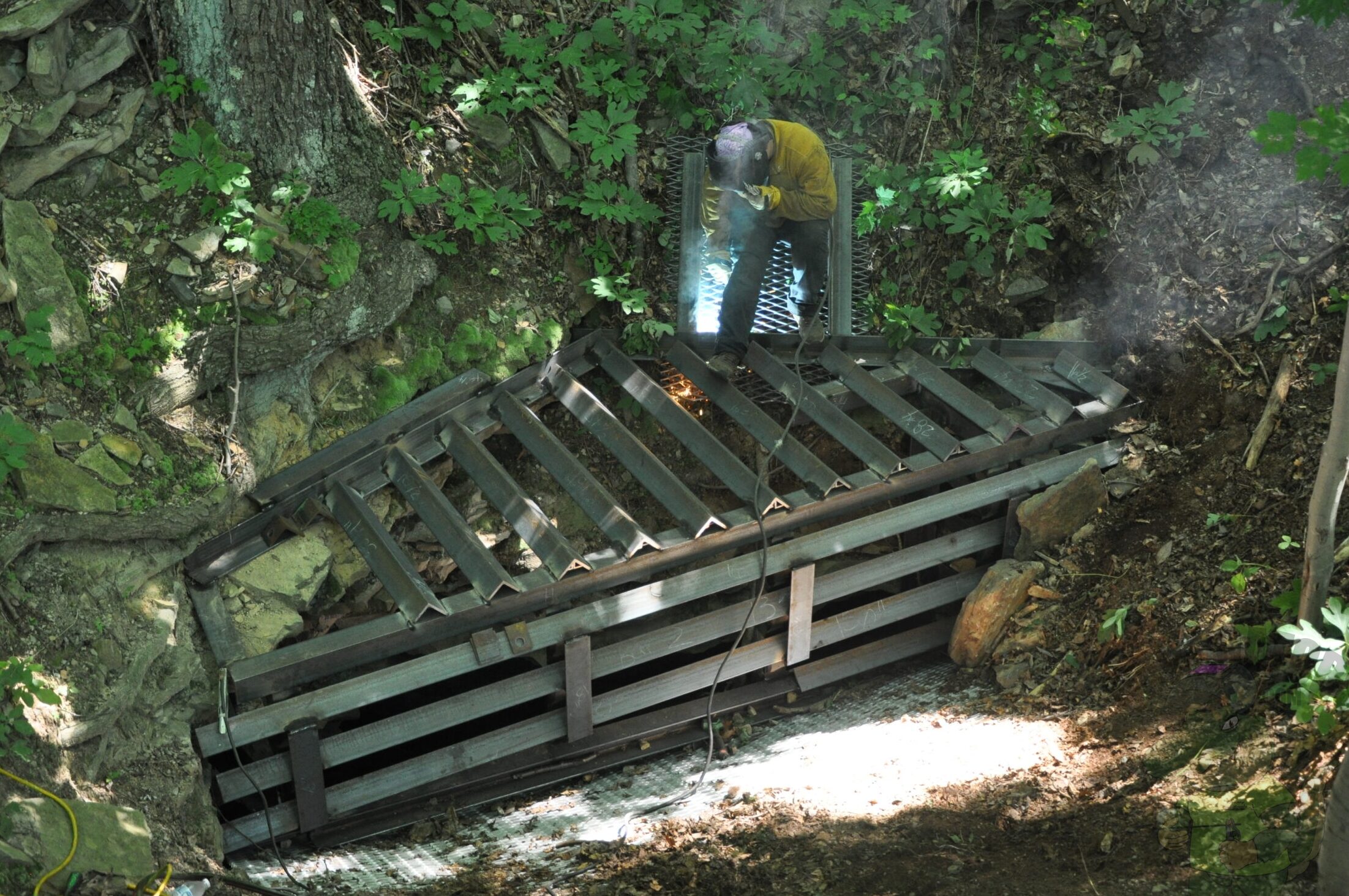
Gating a cave or mine entrance requires careful consideration of the resources and threats present. Factors such as the presence of cultural remains or endangered species, as well as inherent dangers, must be taken into account. If the site can withstand minimal impact, signage may be sufficient to deter visitors. However, if inherent danger is a concern, state laws may already offer protection. It is important to consult an attorney, as in some cases gating may increase liability. Abandoned mines require different considerations.
Why Bat Gates?
Bat-friendly gates come in many styles and modifications, but they are all based on the horizontal angle-iron bar design with 5 3/4″ spacing. This design was developed by Roy Powers, an engineer and avid cave conservationist, after many years of trials and tests. Each gate must be carefully built to fit the opening, anchored to competent bedrock, and constructed to prevent illegal entry and thwart vandalism.
Bat-friendly gates are designed to have no impact on the environment inside the cave or mine, which is important for protecting bat roosts. They also work well for safeguarding sites with important archeological, paleontological, mineralogical, and other biological resources. These gates are the preferred choice of many organizations, including the National Park Service, US Forest Service, US Fish and Wildlife Service, and state wildlife and conservation agencies. They have also been endorsed by the National Speleological Society, American Cave Conservation Association, The Nature Conservancy, and Bat Conservation International.
Placement of gates, and variations on the standard design
After deciding to protect a cave or mine with a gate, there are different gate designs available based on specific criteria. Placement is an essential factor for all gates, and specific criteria may depend on the type of resource to be protected. Gates that are designed to protect bats depend on the type of bat and the season. The standard gate design is effective in protecting other resources like cultural sites and invertebrates.
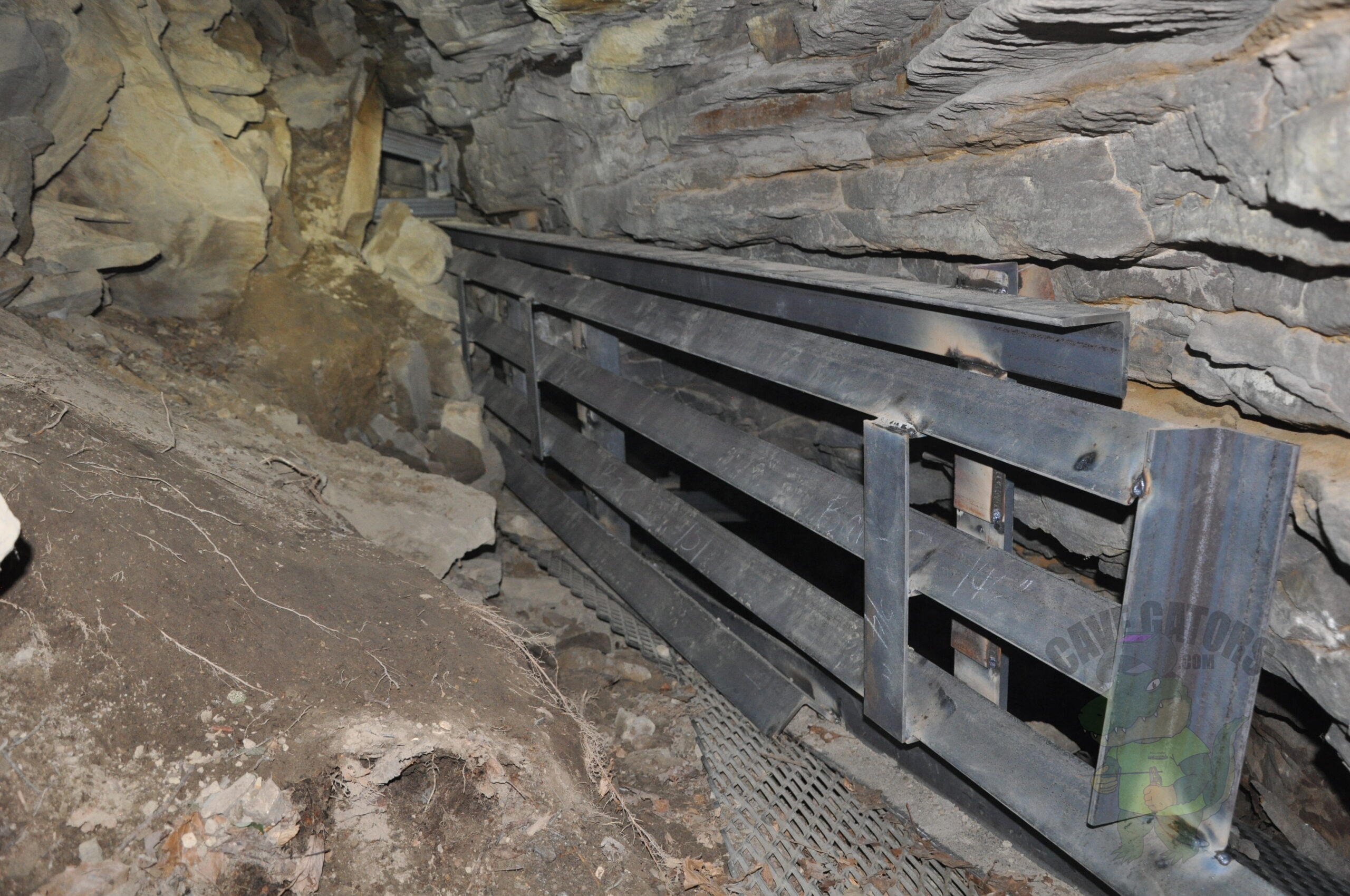
When placing a gate, it should not restrict airflow, and the gate should not be placed in the smallest cross-sectional area to save on material costs. Restricting airflow changes temperature, pressure, and humidity levels, which can have harmful effects on the ecosystem. If bats are present, gate placement should also not obstruct bat flight. Gates should be put in areas of competent bedrock for security and monitoring.
Some caves or mines may require different types or styles of gates, but the basic gate components should remain the same. Consulting with a cave-gating specialist like Cave Gators during the planning phase is highly recommended.
Design
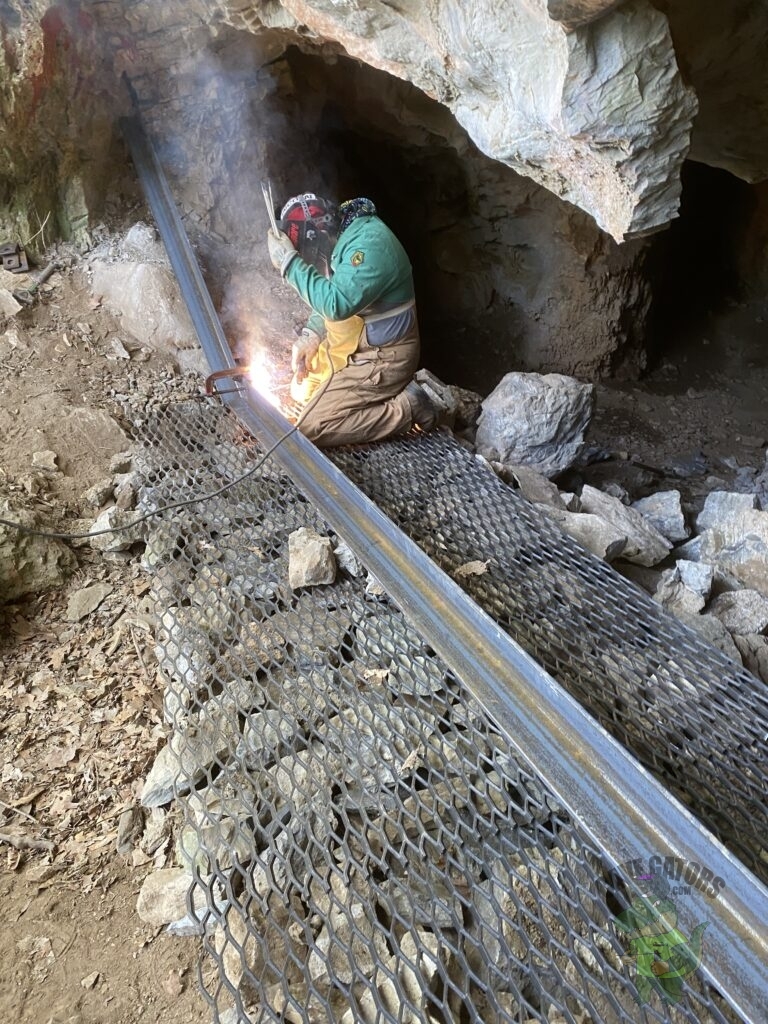
The gate should have a weight-supporting bottom sill spanning the width of the passage, made of 4″ x 4″ x ⅜” or 6″ x 6″ x ⅜” angle iron. Vertical support columns should be connected to the sill at the greatest separation possible, not exceeding 15′ (4.6m). They should rest on solid bedrock or an expanded metal skirt with at least 2 feet of EM3 on both sides of the gate. 4″ x 4″ x ⅜” angle iron footers support the columns and prevent lifting of the expanded metal. The vertical columns should ideally be plumb to the longitudinal axis of the cave but can be off-plumb on the perpendicular axis if necessary.
The gate’s columns and horizontal bars are attached to the cave or mine walls with 1″ cold rolled steel round bar pins that are at least 8″ long. These pins are driven into 1″ holes drilled into solid bedrock walls, at least 6″ deep, and preferably 10″ or more. The pins are then welded to pin plates cut from angle iron with a hole for the pin on one side, which is then welded to the gate.
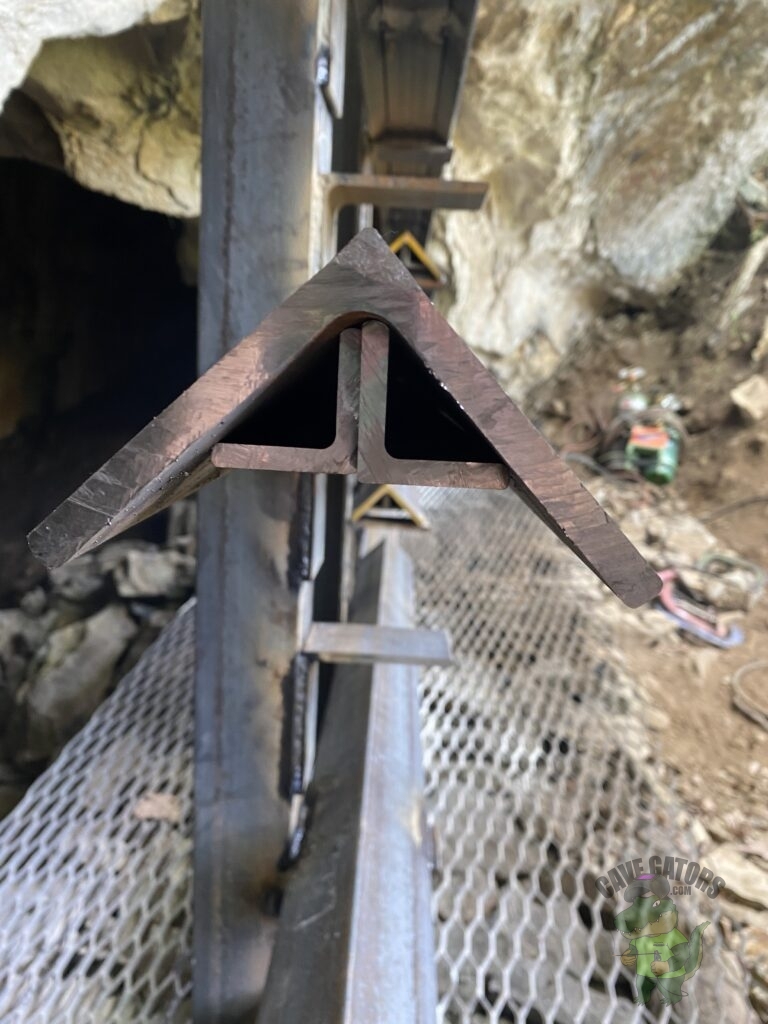
The horizontal bars have two stiffeners inverted and placed inside the 4″ x 4″ angle and welded to the 4″ x 4″ angle every two to three feet of its length. The completed horizontal bar is to be placed on 6″ x 6″ x ⅜” thick flanged angle iron hangers. The hangers are connected to the vertical support columns so that the height from the top of one horizontal bar is 5¾” from the bottom of the bar above it.
A 4″ x 4″ x ⅜” angle iron header bar is welded to the top of the vertical support columns. The bat guard/torsion plate is welded to the front side of the hangers-on on all vertical support columns. The opening or door should be no less than 38″ wide by 14½” tall. This allows a loaded rescue litter to be passed through the gate in case of an emergency. Removable bars (see upcoming diagram) are the most secure but can be unwieldy for high-traffic use. In that case, a hinged door panel may be constructed as an alternative but requires more care in engineering to assure long-term functionality without compromising the structural integrity or security of the gate.
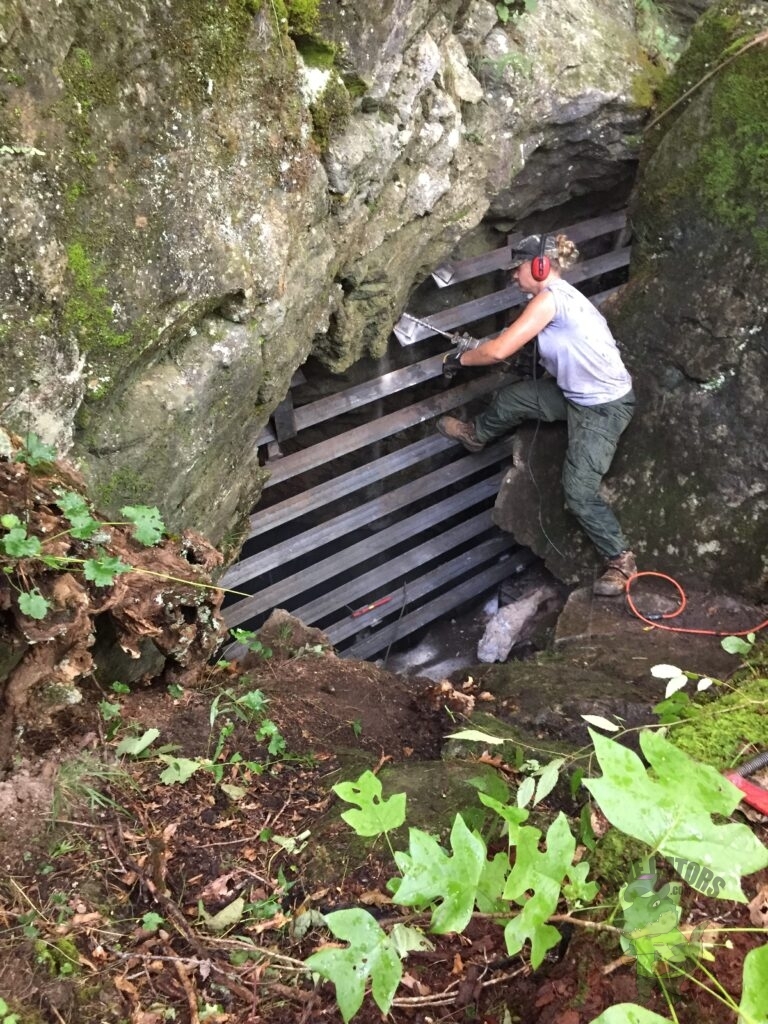
Gates are typically left unpainted. The average projected life of a cave or mine gate is about 20–30 years but may be many more in a dry, stable environment. The lifespan can be substantially less in areas of extreme weathering, or when attached the gate is installed in a corrosive area. Gate designs continue to evolve, and gates need to be replaced as new and better options become available.
Excerpted from Agency Guide to Cave and Mine Gating (2021 edition).